HSM( High speed machining )とは?
HSMはAdaptive Clearingとか負荷制御とも呼ばれています。
一般的には、工具負荷が一定になるようなパスだと言われていますね。
じゃあ、工具負荷が一定とは、どんなパスなのか?
簡単なポケット形状を掘り込むパスを出してみます
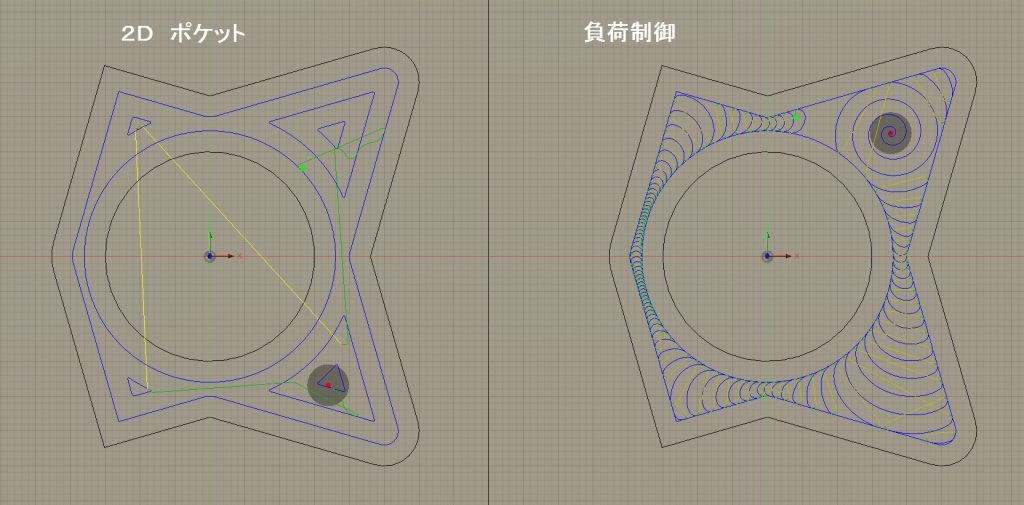
左が「通常ポケット」。右が「HSM」です
ぜんぜん、違いますね~
HSMは加工時間の短縮ができるとの情報もありますが、本当でしょうか?
このパスを見た限りでは、通常ポケットに比べるとかなり複雑で
逆に、時間がかかるように思ってしまいます
実は、どんな場合でも効率よくなるか・・と言われるとそうでもないんです
やっぱり、得意不得意があるので、ある程度特徴をつかんでおく必要があります
HPM(High Performance Machining)と HSM(High speed machining)
「通常ポケット」のパスは、非常にシンプルで経路も短いです
一見、効率的な加工方法に見えなくはないですね
それに対して「HSM」は複雑ですね
実は、切削の負荷を一定にするためにはこんな複雑な動きになるようです
負荷を一定にできるため、横の切込み量は少なくなりますが、加工が安定するため高速に加工する事ができます
効率を取るか?スピードを取るか?
実際の加工時間は、時間あたりの切り屑の排出量できまります。
ゆっくりだけど、一度に沢山削り取るのか(HPM)、少しずつだけど、速く削るのか?(HSM)
どっちの削り方がいいのでしょうか?
これは、加工形状でも違ってきますし、加工機械にも左右されます
力のない機械に、一度に沢山削れ!といっても限界がありますし
スピードの出ない機械に、速く削れと言うのも無理がありますね
やぱり、それぞれの特徴をつかむ事が重要です
実は、旧式の機械で「HSM」で削っても効果は出にくい場合も多いです
切削条件
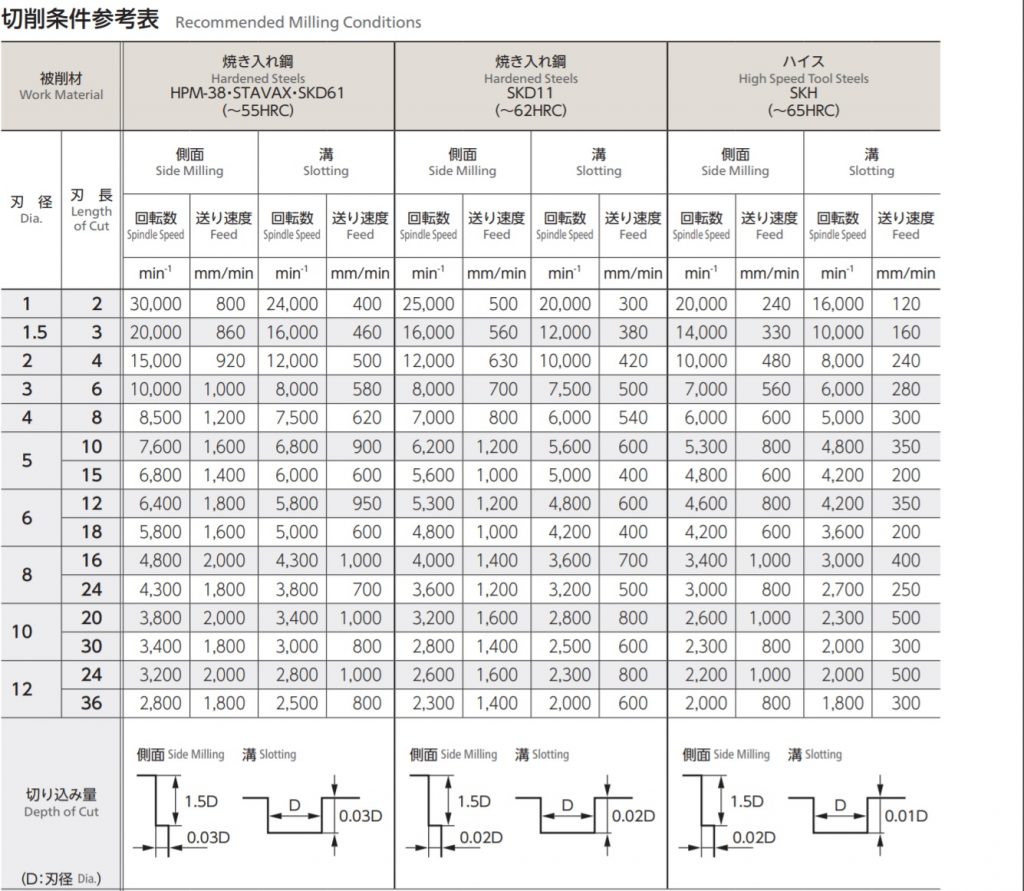
これは、ある工具メーカーの切削条件表です
「側面」と「溝」という項目があります。
一番下の図を見ると、「1.5D」とか「0.03D」とかの指示があります
「1.5D」とは、工具径の1.5倍と言う意味です。
一番左の例では、深さ方向に切り込みは、工具径×1.5 で横方向の切り込みは工具径×0.03の意味です
その「側面」と「溝」の条件に対して、「回転数」と「送り速度」が設定されています
ざっと眺めるとわかりますが、「側面」のほうが2倍近く速いですね
要するに、比較的深い形状で、側面の切込み量が保障されれば、「側面」条件が使えると言う訳です
「 HSM」の場合、この側面の切り込み量が保障されているので、「側面条件」が使えます
「通常ポケット」の場合には、側面切り込み量は一定になりません。
したがって「溝」条件を選択せざるを得ません
ただし浅い形状の場合には、「通常ポケット」のほうが効率がいい場合もあります
加工物素材材質
加工物の材質についても、少し考えてみます
高硬度な材料を削る場合、溝切削ではかなり工具に負担がかかります
したがって、高硬度用のエンドミルの条件は、側面切削条件がほとんとです
おそらく 溝加工では、工具はすぐにダメになってしまいます
したがって深い形状や高硬度の材質を削る場合には、「HSM」は非常に威力を発揮します
エンドミル
切削加工に使用する、エンドミルを見てみましょう
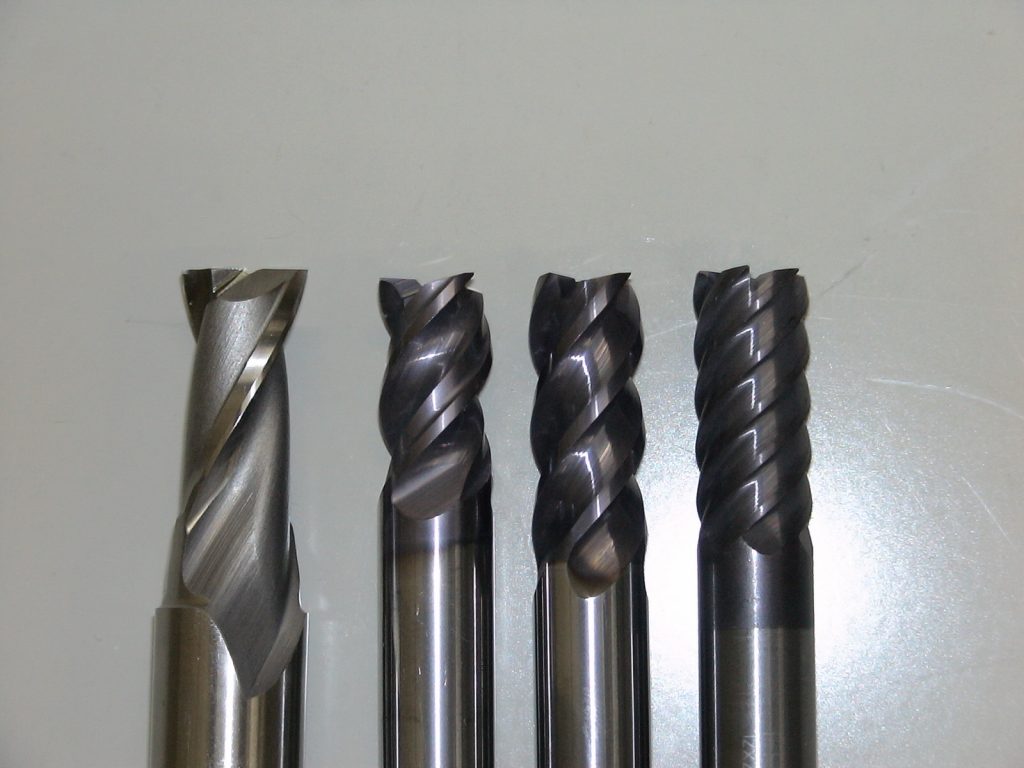
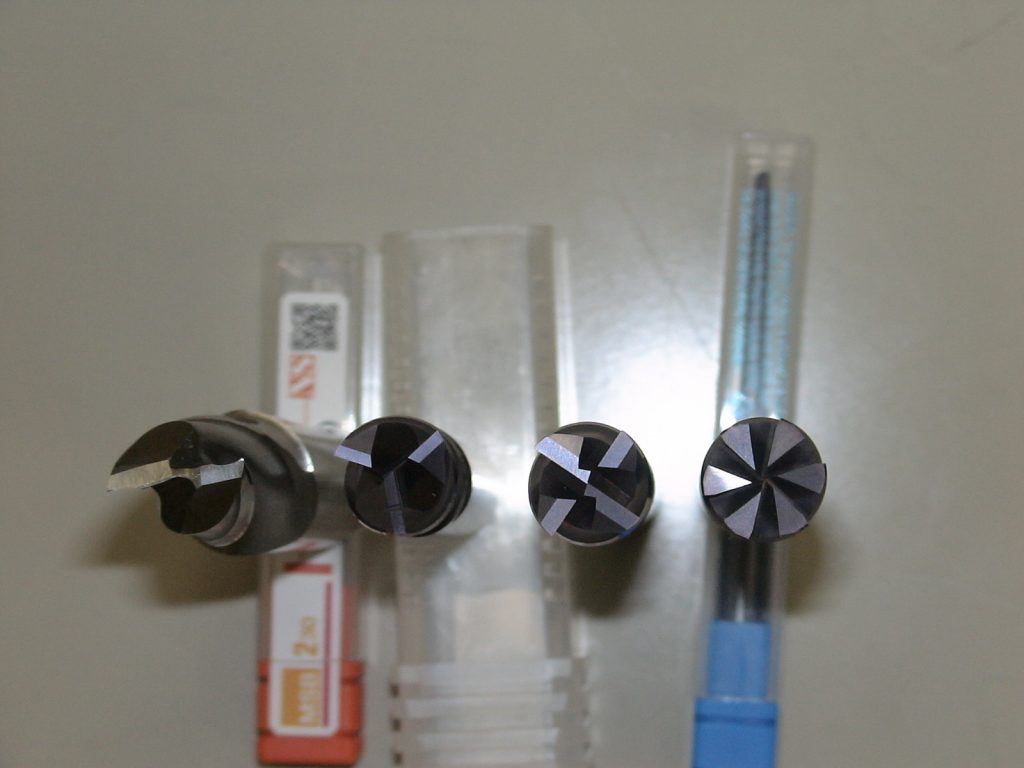
右に行くほど、工具軸に対して螺旋の角度がきつく、芯は太くなっているのがわかります
溝切削の場合は、切り屑の排出をよくしたいので、螺旋がゆるく、刃数が少ないほうが向いています
側面切削は、深切込みで横切込みは少ない条件です。
したがって切り屑厚さは比較的小さいので、 基本的に刃数と速度は比例しますから刃数を多くしほうが、加工速度をはやくできます
「HSM」には、右側の工具形状が向いていると思います
さらに「HSM」は横の切込み量が一定なパスを出してくれますから工具メーカーも理論値で設計できるので幅広い形状を検討できるのではないでしょうか?
その影響か?最近では「HSM」用のエンドミルが市販され、かなり効率的な加工が可能になってきました
トロコイドとHSM
HSMが話題になる前、トロコイド加工という方法が注目されていました
横方向の切込みを一定にするという事では、HSMと似たようなパスですが
トロコイドの進化系がHSMともいえます
トロコイドは横方向の切り込みを一定にする方法ですが
HSMはそれだけはありません、実際に切削している時に
素材と接触している角度(エンゲージ角・切削関与角)も一定にするようです
これにより、切り屑厚さを一定にした加工が可能になります
したがって、最近では加工条件設定を検討する場合、切り屑厚さを基本にして条件設定する工具メーカーさんもあります。
特に、ヨーロッパ系の工具メーカーさんはこの傾向があるようです。
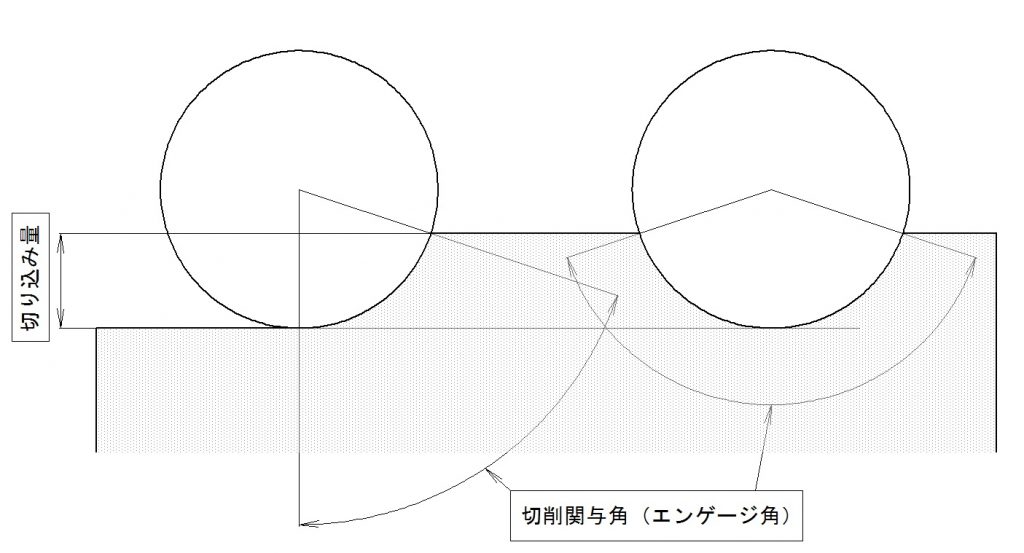
HSMによって、工具の負荷が安定するので、切削理論を元に工具設計ができるのだと思います
安定した加工
加工効率は、加工物形状や機械能力でも影響しますが、ソフト的に安定性を検証してみます
私が使っている、TRYCUTというシミュレーションには、工具が移動する事で加工した
切り屑排出量をグラフ化できるおまけがついています
切り屑の排出が一定なほうが安定した加工といえます
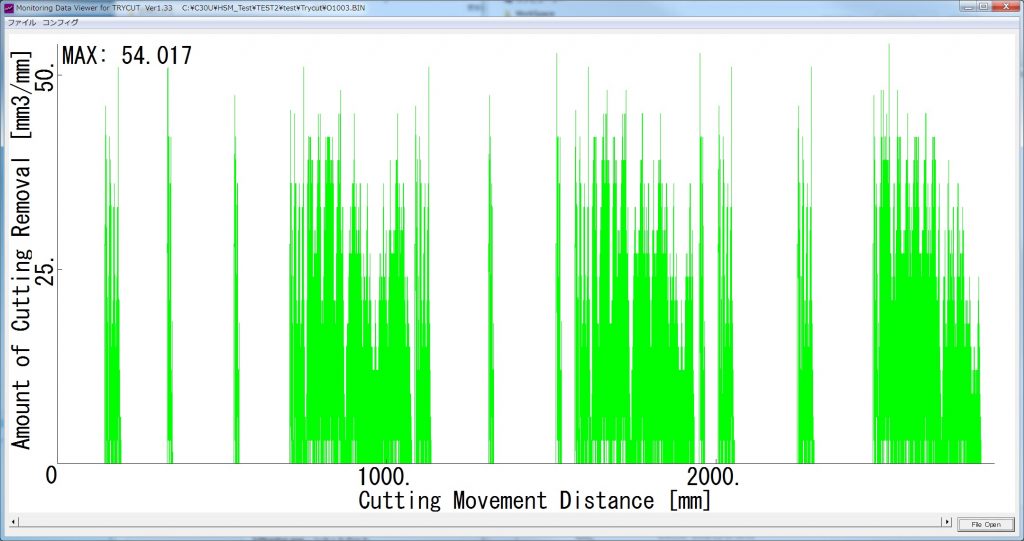
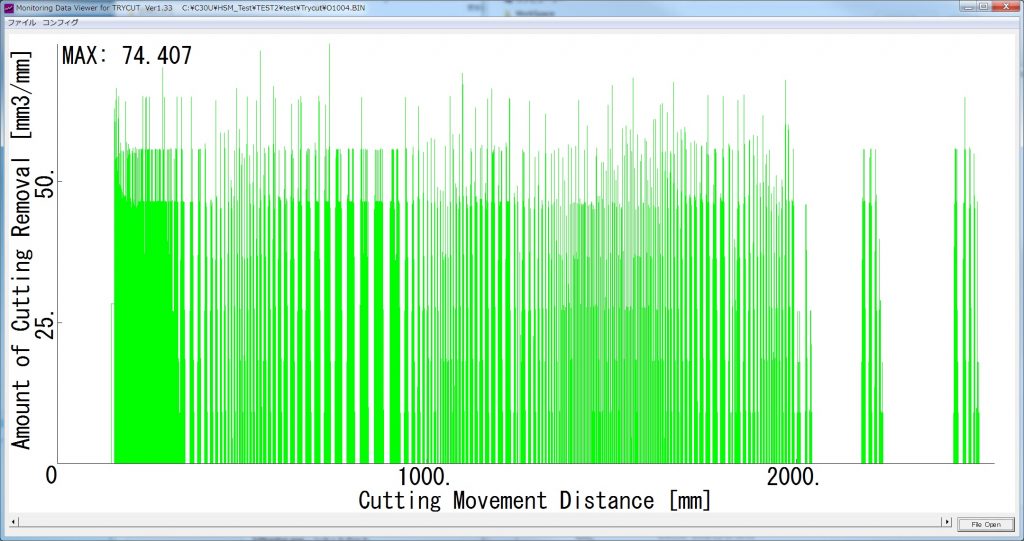
この図形で、上が「通常ポケット」で出力したパスのグラフ
下が「HSM」で出力したパスのグラフ
切り屑排出量が「HSM」のほうが多いのは、工具メーカーのカタログ値によって、削り深さと横の切り込みを設定した結果です
負荷の安定度は一目瞭然ですね!
負荷制御とよばれるのみ分かります。
「通常ポケット」では、一気に仕事したかと思うと、何もしなかったりと負荷が不安定です
「HSM」は常に一定の仕事量ですね
このように安定しているという事は、工具にもやさしく、工具寿命は延びると推測できます。
勘が必要なくなる?かも・・・
加工条件の設定も、経験などに頼らずに、工具カタログを参考に簡単に設定できそうですね。
ここも重要なところです。
加工条件設定は、形状が複雑になるほど、経験が必要になってきますが、負荷が一定な「HSM」なら、あまり形状にとらわれず、新人君でもカタログ片手に条件設定ができそうです。
HSMは荒加工で威力を発揮する
加工形状や加工機の違いにより、「HSM」の効果は違ってきますが
よほど、浅い切り込みでない限り、荒加工は「HSM」で問題ないと思っています
あまり効果がでない状況であっても、負荷の安定は工具にはやさしいですし
常に切削量が一定のパスを出してくれます
また、高回転スピンドルで、剛性がない主軸の機械でも、HSMによりある程度ラフな加工も可能ではないかと思っています
次回、HSK32E 40000rpm の華奢な主軸でのテスト加工をレポートします
Fusion360 の CAM
HSK(負荷制御)は、10年以上前にどこかの展示会の「SolidCAM」のブースでみてから、ずっと気になっているパスでした。
だたどうしても、このパスだけのために新CAMを導入する事はできませんでしたが、最近導入した「Fusion360」は、年間6200円のサブスクながら、この機能が使えます。
たぶん、「SolidCAM」などのCAMに比べれば、機能的には基本的なものだけだと思いますが、形状によっては、通常の削り方よりも、かなり効果がでています。
次回は、Fusion360 負荷制御の事例を紹介します。
また、Fusion360 CAM の使用方法などの記事も書き始めましたので、ご興味あればご覧ください
コメント